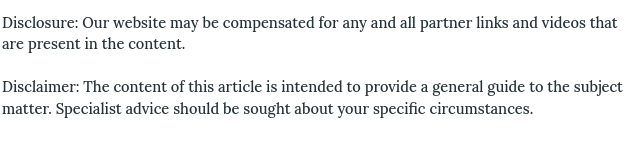
It may or may not come as a surprise that of all manufacturers out there, 70% of them have a compressed air system. Compressed air distribution is a very big part of what they do, and having a compressed air piping design that is poorly done can severely deter a manufacturer from being as efficient as it needs to be. The delicate piping that allows for a standard amount of pressure can break, become clogged, or lose flexibility over time.
A common error that is found in compressed air systems is line sizes that are too small for the desired flow of air. This involves the interconnecting of the piping from the compressor discharge to the dryer to the header. In addition, it applies to the distribution lines that convey air to different production areas and within the equipment found in these areas. Proper air piping design takes this into consideration. The piping should be the size of the air flow that is needed for effective production.
If you have undersized piping, the flow of the air is restricted and this reduces the discharge pressure. When this occurs, the user is robbed of compressed air power, which is costly. These kinds of poor piping practices increase velocity and turbulence-induced back pressure. With reduced air power thanks to poor air piping design, you could be losing valuable time and money.
Pipe size and layout design are the most important variables in moving air from the compressor to the point of use. Poor systems not only consume significant energy dollars but also degrade productivity and quality. Artificial demand is created as a result of pipes that do not fit well in a poorly conceived compressed air piping design.
Artificial demand is created when the end use is supplied more air pressure than is needed for a particular application. If for example, a particular application requires 45 PSI but an air compressor supplies 85 PSI, the excessive air pressure is still going to be used, and that is costly in the end. A compressed air distribution system that functions poorly in this way can cost manufacturers thousands of dollars a year in wasted energy bills.
Air compressor piping leaks can be very costly and can sneak up on a company that is not prepared to spot them. A 1/8 inch diameter hole in a 100 PSI system can cost a company upwards of $1,200 per year in energy that is wasted. That is why it is well worth the time and expense to maintain air compressor systems and fix any sizable leaks before they do too much damage. As they say, an ounce of prevention is worth a pound of cure. By addressing leakage and being proactive about potential poor air piping design, who can prevent unnecessary shut downs and expensive repairs in the future.
The US Department of Energy does annual energy audits, and it has found that over 50% of compressed air systems have a number of low-cost energy options that companies can employ to make the most of their compressed air piping design. In employing these low-cost energy options, companies can not only save money but make significant contributions to the conservation of energy on a larger scale.
What it all comes down to in the end is the control of air pressure loss. Compressed air piping design that results in a compressor that is efficient will see pressure loss that is no greater than 10% of the compressor’s discharge pressure. This can be kept track of by a gage found on the compressor’s outlet. Of course, there is not a piece of equipment more important than the human eye. By paying attention to output and pressure readings you will be able to ensure your equipment is working properly.
Related Topics:
air compressor copper pipe fittings, air compressor design guide, air compressor piping setup, air compressor sketch, air compressor system diagram, air compressor to tank pipe, air compressor to unclog pipes, air flow in pipe pressure drop, air flow rate through pipe given pressure, air flow through a pipe calculator, air flow through pipe, air header schedule, air hose pressure drop chart, air line pipe and fittings, air line pipe size, air pipe calculator, air pipe installation, air pipe line calculation, air pressure drop calculation formula, air pressure pipe, air receiver design.
Related Keywords:
air compressor copper pipe fittings, air compressor design guide, air compressor piping setup, air compressor sketch, air compressor system diagram, air compressor to tank pipe, air compressor to unclog pipes, air flow in pipe pressure drop, air flow rate through pipe given pressure, air flow through a pipe calculator, air flow through pipe, air header schedule, air hose pressure drop chart, air line pipe and fittings, air line pipe size, air pipe calculator, air pipe installation, air pipe line calculation, air pressure drop calculation formula, air pressure pipe, air receiver design.